Consultation
The Premier Consultation Hub for Industrial Rotating Equipment Excellence
Our Finite Element Analysis (FEA) and Computational Fluid Dynamics (CFD) consultation services offer a comprehensive suite of solutions tailored to your specific engineering and design demands. Whether you’re striving for structural integrity, thermal optimization, or fluid dynamics insights, we understand your unique needs and guide you through every step of the process.
Consultation
Finite Element Analysis (FEA)
Computational Fluid Dynamics (CFD)
Finite Element Analysis (FEA)
FEA services in rotating equipment provide valuable insights into critical components’ structural integrity, performance, and reliability. By leveraging advanced simulation techniques, engineers can optimize designs, reduce the risk of failures, and ensure the efficient operation of rotating machinery in various industries.
Dynamic Analysis
FEA is employed to conduct dynamic analysis of rotating equipment, such as pumps, turbines, or rotors. It involves studying the response of components to varying loads, including centrifugal forces, vibrations, and rotational speeds.
Stress and Fatigue Analysis
Rotor Dynamics
FEA is utilized to study the behavior of rotating shafts and associated components, analyzing critical factors like natural frequencies, mode shapes, and stability to prevent resonance and ensure smooth operation.
Bearing Analysis
Thermal Analysis
Fluid-Structure Interaction (FSI)
In cases where rotating equipment interacts with fluids, FSI is employed to study the impact of fluid forces on structural components. This is relevant in applications like pumps or fans where fluid dynamics influence structural behavior.
Vibration Analysis
Failure Mode Analysis
FEA assists in predicting and preventing failure modes in rotating equipment. Engineers can identify potential failure points by simulating different operating conditions and implementing design improvements to enhance reliability.
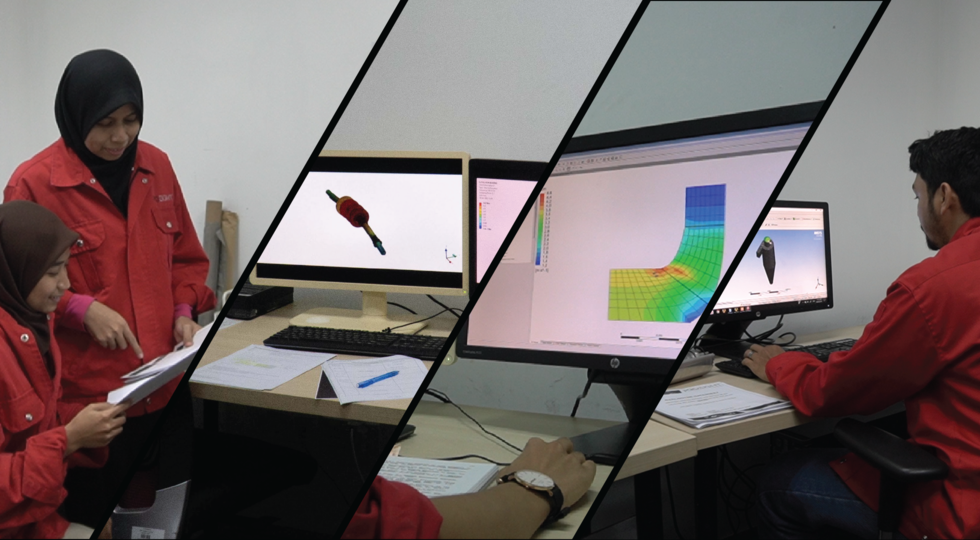
Computational Fluid Dynamics (CFD)
Computational Fluid Dynamics (CFD) is a powerful engineering discipline that utilizes numerical methods and algorithms to analyze and simulate the behavior of fluids (liquids and gases) and their interactions with solid structures. This advanced computational tool is instrumental in understanding and optimizing fluid flow, heat transfer, and related physical phenomena in various industry applications.
Computational Fluid Dynamics (CFD) analysis finds diverse applications in rotating equipment across various industries. Here are several vital applications where CFD is commonly employed in the study and optimization of rotating machinery:
Pump Performance Optimization
CFD helps optimize the design of pumps by analyzing fluid flow within impellers, volutes, and other components. This includes evaluating pressure distribution, flow rates, and efficiency to enhance pump performance.
Centrifugal Separator Performance
CFD assists in analyzing the separation efficiency of centrifugal separators. It provides insights into fluid dynamics within the separator, allowing engineers to optimize designs for improved particle separation and reduced energy consumption.
Bearing and Lubrication Systems
CFD is utilized to analyze the fluid dynamics within bearings and lubrication systems of rotating equipment. This includes studying oil flow and pressure distributions and optimizing designs to reduce friction and wear.
Hydraulic Turbines and Pumps
CFD is applied to study the fluid flow in hydraulic turbines and pumps. This involves analyzing efficiency and cavitation risks and optimizing designs for improved hydropower and water management systems performance.
Fan and Blower Design
CFD analyzes the aerodynamics of fan blades and impellers in HVAC systems, industrial fans, and blowers. This includes studying airflow patterns and pressure distributions and optimizing blade designs for improved efficiency and reduced noise.
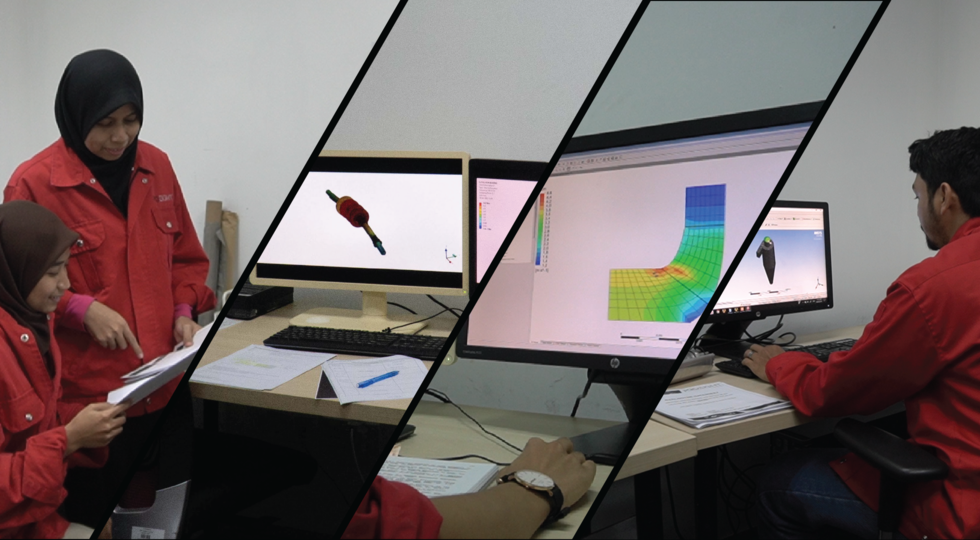